Drilling is a crucial activity during the mining process, which, if not controlled, will generate large amounts of dust. Dust will reduce the operator’s visibility and equipment lifespan. Dust also impacts workers’ productivity and causes environmental, health, and safety problems. This article will review the main surface drilling techniques and dust control measures for different soil and weather conditions.
Introduction to Surface Drilling Techniques
Surface mine drilling is an essential process involving both rotary and percussion drilling methods. Rotary drilling combines rotation and high down-pressure to penetrate rock using a column of drill pipe with a roller drill bit. On the other hand, percussion drilling employs a pneumatic drill with a piston that delivers hammer blows for rock penetration. Each technique has unique requirements and outcomes vital for effective surface mining operations.
Understanding Dust Control in Surface Drilling
Effective dust control in surface drilling is crucial for health and environmental reasons. Methods like wet or dry drilling with dust collection systems are commonly employed. These techniques adapt to the specific operational environment and drilling equipment, ranging from small crawler rigs to large track-mounted drill rigs.
Wet Drilling
An Efficient Dust Control Strategy
Wet drilling stands out for its high dust control efficiency, reaching 96 percent. It involves injecting water with air to flush cuttings, requiring careful monitoring to balance dust control and operational effectiveness. Optimizing water flow rates, typically between 0.1 and 2.0 gallons per minute or 0.35 to 7 liters per minute, is crucial to maximize dust control while avoiding operational issues like drill bit plugging or hole collapsing.
Advantages and Recommendations for Wet Drilling
Besides dust control, wet drilling can potentially increase the penetration rate in surface mining. Recommendations for optimal wet drilling include gradual water increase to minimize dust emissions, continuous monitoring, and using filtered water combined with polymers and surfactants. Polymers and surfactants will reduce the water needed for dust control, improve hole preservation, and facilitate the work. They can work best for dry and loose soil. However, the system must be heated or drained in cold temperatures to prevent freezing.
Challenges and Solutions in Wet Drilling
One significant disadvantage of wet drilling, especially in rotary drilling, is the rapid degradation of tri-cone roller drill bits, as well as the increase of weight in the soil material if too much water is added. A solution to this is effective water optimization and separation, preventing water from reaching the drill bit and extending its life.
Water Separator Sub: Enhancing Dust Control and Bit Life
The water separator sub is an innovative solution that separates water from the bailing air, thus preventing slurry formation at the drill bit and enhancing dust control efficiencies. This technique also significantly improves drill bit life, a crucial factor in reducing operational costs.
Employing diluted polymers in conjunction with the water separator sub for dust control in mining operations is a prudent strategy for several reasons. The diluted polymer solution, when combined with the water separator sub, enhances the efficiency of dust suppression by optimizing the separation of water and air. The use of diluted polymers facilitates improved coverage over dust-prone areas, maximizing the binding capacity of the polymers with airborne particles.
The water separator sub, operating on the principle of inertia, efficiently removes water from the bailing air, ensuring that the dust control system remains focused on addressing particulate matter. This combined approach not only promotes effective dust control but also minimizes the overall consumption of water and polymer resources, contributing to cost-effectiveness and environmental sustainability.
Explore innovative dust suppression solutions
Top reasons why reducing dust emissions by 99% should be a company’s main goal
Addressing Specific Challenges in Quarrying and Drilling
In the context of quarrying and drilling, especially in materials like iron, copper, nickel, gold, and other minerals, controlling the particle sizes of dust is crucial. Employing techniques like wet drilling and using advanced equipment such as cordless drills, turbo drills, and vacuum systems can significantly enhance dust control measures. As automatization advances, autonomous drills are starting to enter the market., is important to remark that Autonomous drills work better with proper visibility and dust control measures.
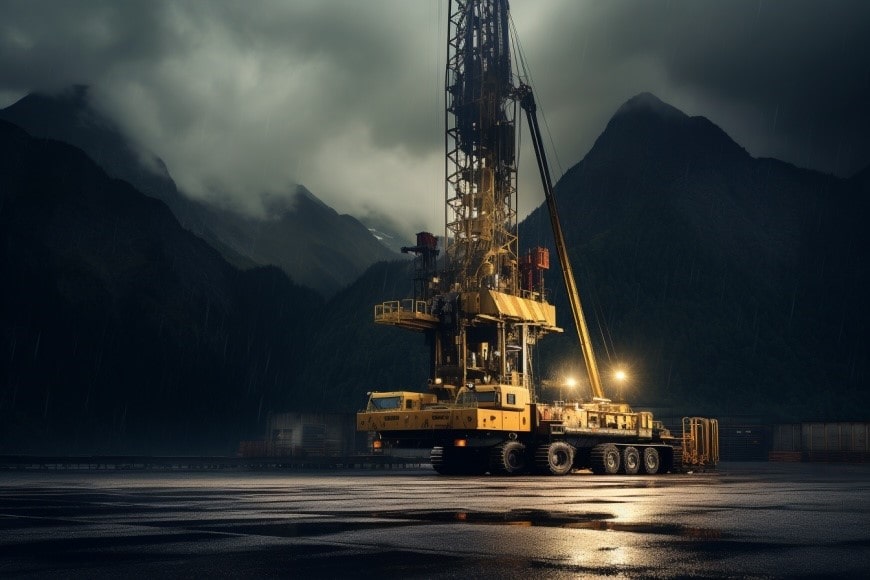
Dry Drilling
Overview of Dry Drilling
Dry drilling is a method that omits water in the dust control process. It relies on fan-powered dust collection systems attached to the drill, which can operate in various climates. When properly maintained, these systems can achieve up to 99% efficiency in dust control.
Medium- to Large-Diameter Drill Dust Collection Systems
The bailing air plays a crucial role in dust generation for medium- to large-diameter drills. The dust collection system consists of an exhaust fan and filters. The air, laden with dust, is drawn from under the shroud to the filters, which are periodically cleaned by backflushing. This system is designed to contain and capture dust effectively, but its efficiency can be compromised by gaps around the shroud or drill deck.
Sources of Dust Emissions from Collection Systems
The integrity of the dust collection system is vital. Common issues leading to dust emissions include damaged filters, worn enclosure components, or operational challenges affecting the system’s ability to contain and capture dust.
Tackling Deck Shroud Leakage
Deck shroud leakage is a significant challenge in dry dust collection. Modifications such as corner flaps or a single-piece shroud can improve sealing and reduce leakage. The design of the shroud, whether rectangular or circular, plays a significant role in its effectiveness.
Circular vs. Rectangular Shrouds
Circular shrouds, conical in design, offer a seamless and effective solution for dust capture. They can be hydraulically adjusted to maintain contact with the ground, reducing leakage significantly. However, adjustments might be necessary during drilling to prevent cuttings from re-entering the hole, thereby temporarily breaking the seal.
Collector-to-Bailing Airflow Ratio: A Key Performance Indicator
The ratio of the collector to bailing airflow (QC/QB) is critical for dust collection performance. Maintaining an appropriate ratio ensures efficient dust capture. Changes in this ratio can significantly affect dust levels. Regular monitoring and adjustments based on field conditions are essential for optimal performance.
Maintaining Airflow for Effective Dust Control
Regular maintenance of both the bailing airflow and the dust collector is crucial to sustaining high collector-to-bailing airflow ratios. This involves:
- Ensuring proper backflushing of filters.
- Checking for leaks and damage in the intake duct and collector housing.
- Regularly replacing filters.
- Keeping the collector fan in optimal condition.
- Monitoring and adjusting the airflow based on field conditions and filter loading.
Conclusion: Wet Drilling vs. Dry Drilling in Surface Mining
The choice between wet and dry drilling in surface mining operations hinges on various factors, including environmental conditions, operational requirements, and health and safety considerations. Both methods have distinct advantages and challenges, and the selection often depends on the specific needs and constraints of the mining operation.
Wet Drilling: High Efficiency with Water Management Challenges
Wet drilling is highly effective in dust control, achieving up to 96% efficiency. The process involves injecting water into the drilling mechanism, which helps suppress dust particles. This method is particularly beneficial in environments where water is readily available and can be managed effectively. However, it requires careful monitoring and optimization of water flow, as well the use of polymers is recommended, to prevent operational issues like drill bit plugging and hole collapse. Additionally, in colder climates, the risk of freezing can pose a significant challenge, requiring additional measures to ensure the smooth functioning of the system.
Dry Drilling: Versatile and Efficient in Diverse Climates
On the other hand, dry drilling uses fan-powered dust collection systems to control dust emissions. This method can be up to 99% efficient if adequately maintained, and it is particularly advantageous in areas where water is scarce or in freezing temperatures where wet drilling may not be feasible.
Dry drilling systems must be carefully designed to ensure effective dust capture, with particular attention paid to the integrity of shrouds and the maintenance of the dust collection equipment. The collector-to-bailing airflow ratio is a critical factor in the efficiency of dry drilling operations, requiring regular monitoring and maintenance for optimal performance.
Key Considerations in Choosing Drilling Methods
- Environmental Conditions: Wet drilling is more suitable in warmer climates, while dry drilling is advantageous in colder or drier regions.
- Operational Efficiency: Both methods require careful management—water flow in wet drilling and airflow ratios in dry drilling—to maintain efficiency.
- Type of soils combined with weather conditions, such as dry soils might require the use of wet dust control measure, while more wet solis might be done with the use of wet control measures combined with our selection of polymers for dust control and soil stabilization.
- Health and Safety: Effective dust control is paramount in both methods to protect workers from respiratory hazards like silicosis.
- Equipment Maintenance: Wet drilling requires managing water systems and preventing freezing, whereas dry drilling demands regular maintenance of dust collectors and air systems.
- Compliance with Regulations: Adherence to environmental regulations and workplace safety standards is crucial in both methods.
Both wet and dry drilling have unique advantages and are suited to different contexts. The decision to use one method over the other should be based on thoroughly evaluating these factors, ensuring operational efficiency and compliance with health, safety, and environmental standards.
What are the soil stabilization techniques and soil stabilization methods?
Dust Master Systems (DMS®) by ABCDust
Dust Master Systems (DMS®) provides a comprehensive range of cutting-edge dust monitoring and suppression solutions tailored for diverse industries, including mining, forestry, and construction. DMS® polymer dust control products stand out for their exceptional dust suppression capacity, enhancements in soil stabilization, water conservation, reduced braking distances, and minimal maintenance costs.
Key benefits of Dust Master Systems (DMS®) include:
- 95-99% proven dust reduction;
- 80-90% water savings;
- Rapid dilution and applications;
- Non-slippery roads;
- Neutral PH. Non-corrosive to machinery;
- Applicable to all types of soil;
- Designed for high traffic of heavy machinery;
- Non-toxic products;
- Water-repellent. Resists impact of rain and snow;
- Harmless to the environment;
- Measured performances to best match different traffic, soil, weather, and water characteristics.
Leveraging the benefits of DMS® suppressant additives allows users to address dust emission at the forefront of the control hierarchy, maximizing effectiveness while also reducing operational costs (such as fuel, tires, water consumption, and corrective maintenance) and enhancing productivity (with increased operating speeds, reduced interference in road maintenance, and shorter cycle times for off-road haul trucks). For more information on tackling the root causes of dust emission and ensuring safety and operational efficiency in mining activities, contact ABCDust.